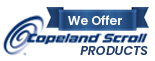
This design ensures good sealing between the scroll spirals. It allows the scroll spirals to contact and separate along the radial and axial directions.
High Efficiency "Teflon" is used for the upper main and drive bearing. "Space age" materials used in the compressor include: (1) Porous bronze (2) PTFE-lead overlay
The scroll spirals in a scroll compressor wear in, rather than wear out. Over time, the wear-in improves performance.
After shut down, the two scroll forms are separated from each other. This enables full internal pressure equalization at shut down.
Refrigerating capacity data listed in this manual are applicable for power frequencies of 50Hz (speed of motor equals 2900rpm) and 60Hz (speed of motor equals 3500rpm).
The scroll design creates a smooth sound spectrum and better sound quality. The layout of the compression chambers is symmetric, making for very minimal imbalances.
A built-in relief pressure valve is mounted between the highpressure and low-pressure side of the compressor.
Both ZB92 and ZB11M motor protection systems include an external protection module for the motor.
Therm-O-Disc (TOD) or ASTP is a temperature-sensitive snap disc device installed at the scroll outlet.
Cut-off the power supply of the control circuit, and bypass the motor protection module.
Cut-off the control circuit and the power supply of the module, and remove the lead wire of the sensor from S1 and S2 terminals of the module
The number of times a compressor can start and stop within a period of one hour depends on the system configuration to a great extent.
If the system design does not ensure compressor operation within the range specified or if the system layout is not reasonable..
Single-phase scroll compressor does not require installation of a crankcase heater. a crankcase heater is necessary
Copeland scroll compressor has a greater capacity to resist liquid because of some inherent characteristics.
To ensure the safe operation of the refrigeration system, Emerson suggests that all systems be equipped with high- and low-pressure switches.
The filter drier installed in the liquid piping should be large enough and adequate for uninterrupted operation.
Installation of the compressor should be done according to the service conditions.